Dive Into the World of Light Weight Aluminum Casting: Comprehending the Different Approaches
Light weight aluminum casting is a fundamental process in the production sector, with different methods used to create specific and complex components. Understanding the different techniques made use of in light weight aluminum casting can give useful insights right into the capabilities and restrictions of each method. From the conventional sand spreading technique to the advanced die spreading process, each technique uses unique benefits depending on the needs of the job. Checking out these diverse techniques can offer a thorough view of the opportunities within the world of aluminum spreading and how each method adds to shaping the modern-day production landscape.
Sand Casting Technique
Sand spreading, a widely-used approach in aluminum casting processes, entails producing molds made of compacted sand for putting molten metal. When the mold is ready, it is firmly positioned in a flask and molten light weight aluminum is poured right into the tooth cavity.
After the metal has cooled and solidified, the sand mold is damaged away to reveal the aluminum casting. Sand casting allows for the production of complicated forms and big components that may be hard or pricey to create making use of various other techniques. It is additionally a sustainable technique as the sand can be reused and used several times, lowering waste in the casting process.
Permanent Mold And Mildew Strategy
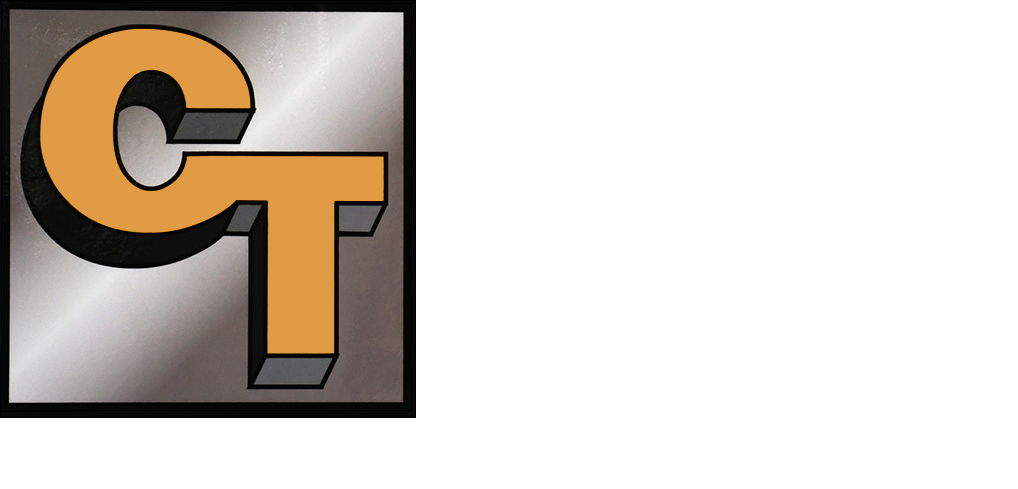
One considerable benefit of the Long-term Mold Strategy is the enhanced dimensional precision it uses. The metal mold permits tighter resistances and finer details in the final aluminum spreadings contrasted to sand casting approaches. This precision makes it a recommended choice for applications where limited dimensional control is critical, such as in the aerospace and vehicle industries.

Pass Away Casting Refine

Financial Investment Casting Strategy
Making use of an accuracy spreading technique, Financial investment Casting Approach includes developing intricate aluminum components by putting molten metal right into a ceramic mold. This procedure, likewise understood as lost-wax casting, begins with the creation of a wax pattern of the desired part (aluminum casting).
The next step entails pouring the liquified aluminum right into the ceramic mold. The light weight aluminum fills up the tooth cavity left by the wax pattern, taking its shape precisely. This approach is favored for its capability to create intricate forms with high precision and a smooth surface area finish. Investment spreading is commonly used for making elements in sectors where limited resistances and intricate designs are required, such as aerospace, auto, and clinical devices. The versatility and accuracy of the Financial investment Casting Method make it a valuable strategy in the globe of light weight aluminum casting.
Lost Foam Spreading Method
Having actually explored the elaborate precision best site of Investment Casting Method, the emphasis currently changes to the cutting-edge approach of Lost Foam Casting in aluminum component production. Lost Foam Spreading, also known as evaporative pattern spreading, is a modern-day method where a foam pattern of the desired component is produced and then covered with a refractory material.
Furthermore, Lost Foam Casting is an affordable procedure as it decreases the need for cores and allows for the production of light-weight components. In spite of its benefits, Lost Foam Spreading requires careful control of the casting procedure to make certain and prevent problems top quality elements.
Verdict
In verdict, aluminum casting offers a variety of methods such as sand casting, permanent mold technique, die spreading, financial investment casting, and lost foam spreading. Each approach has its own advantages and applications, making aluminum casting a versatile and widely used process in various industries. Understanding the distinctions between these techniques is essential in selecting one of web link the most ideal spreading technique for particular manufacturing needs.
Sand spreading, a widely-used technique in aluminum casting processes, entails producing molds made of compressed sand for pouring molten steel. aluminum casting.The Irreversible Mold And Mildew Technique, like sand casting, is an additional prevalent approach utilized in aluminum spreading processes, using unique advantages in terms of mold and mildew reusability and dimensional accuracy. The metal mold and mildew allows for tighter tolerances and finer information in Go Here the final aluminum castings contrasted to sand spreading methods. The 2 major kinds of die spreading are cool chamber die spreading and hot chamber pass away casting, each ideal for various kinds of aluminum alloys.In verdict, light weight aluminum casting offers a variety of approaches such as sand spreading, irreversible mold and mildew strategy, die spreading, investment casting, and lost foam casting